OUR APPROACH
From visualizing the initial concept to the final production of the wheel, we’ll be there every step of the way to help you design your wheels from scratch, to the exact requirements you need and want.
THE FORGED DIFFERENCE
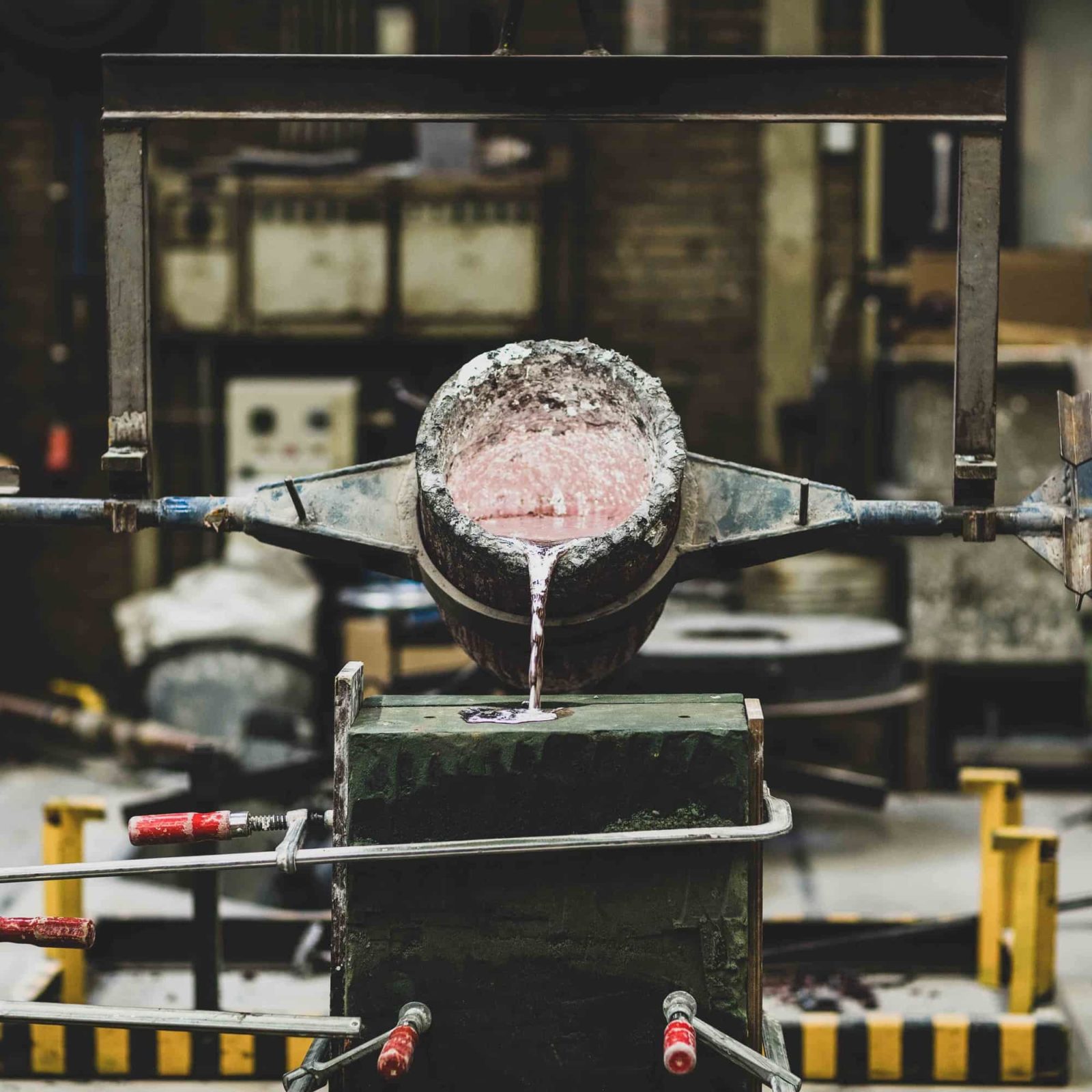
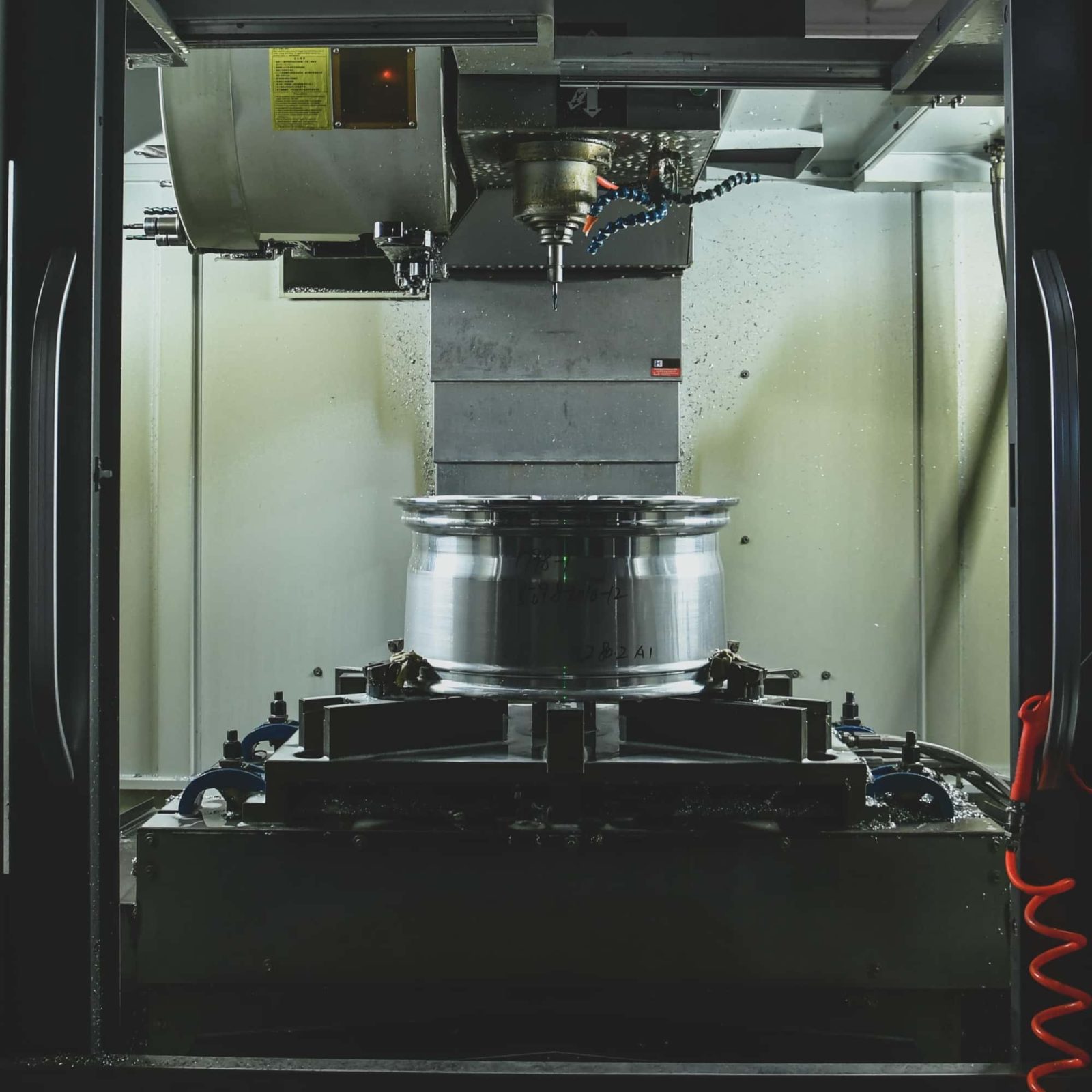
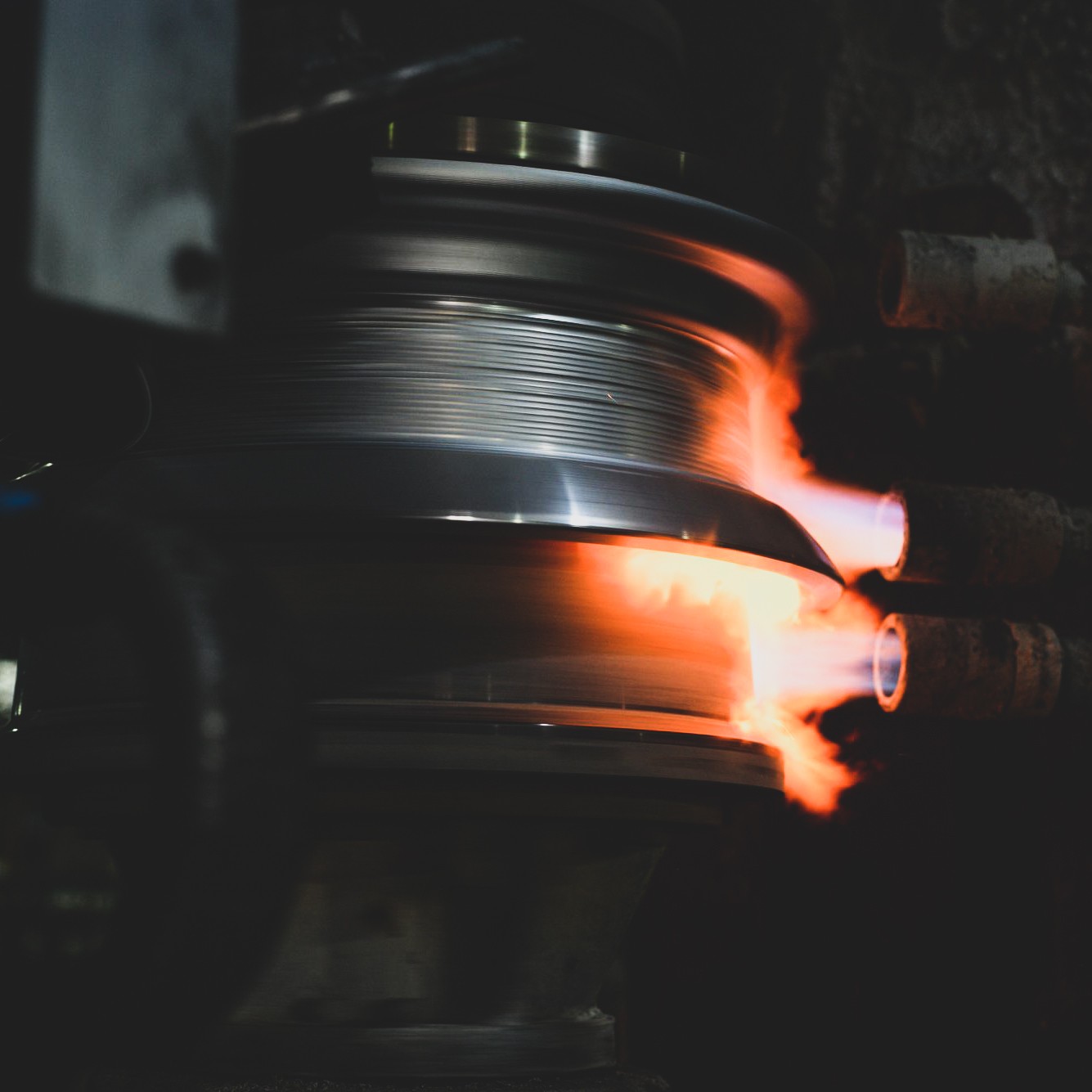
OUR MANUFACTURER
We have vetted numerous manufacturers across North America and Asia in order to partner with one that can meet our strict product standards. Our eventual goal is to bring wheels manufacturing to Vancouver and gain complete control over production from the start to the final packaging. We appreciate everyone’s support on this journey to become the very best Canadian aftermarket wheel manufacturer.
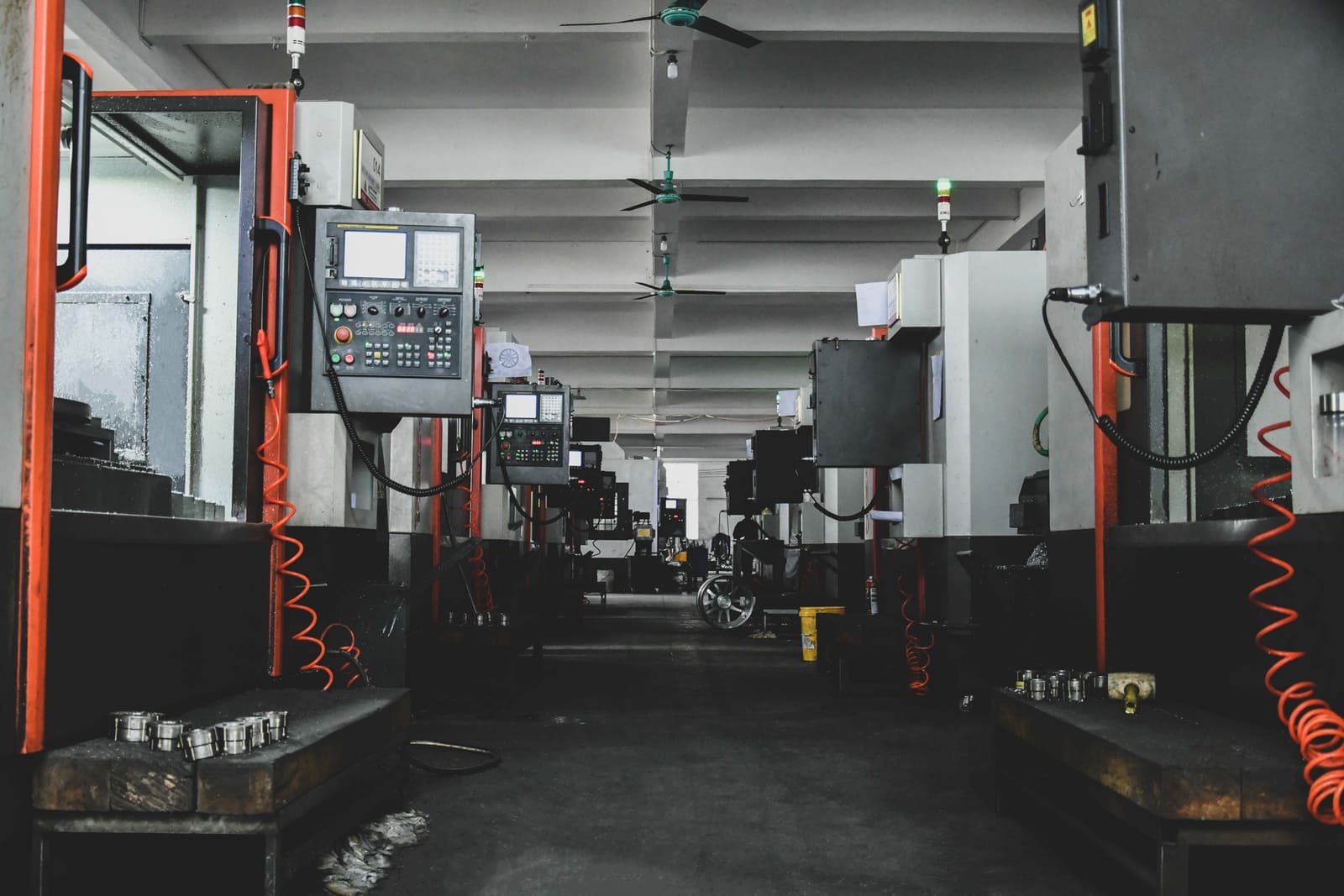
Figure 1. High-speed vertical milling centre array.
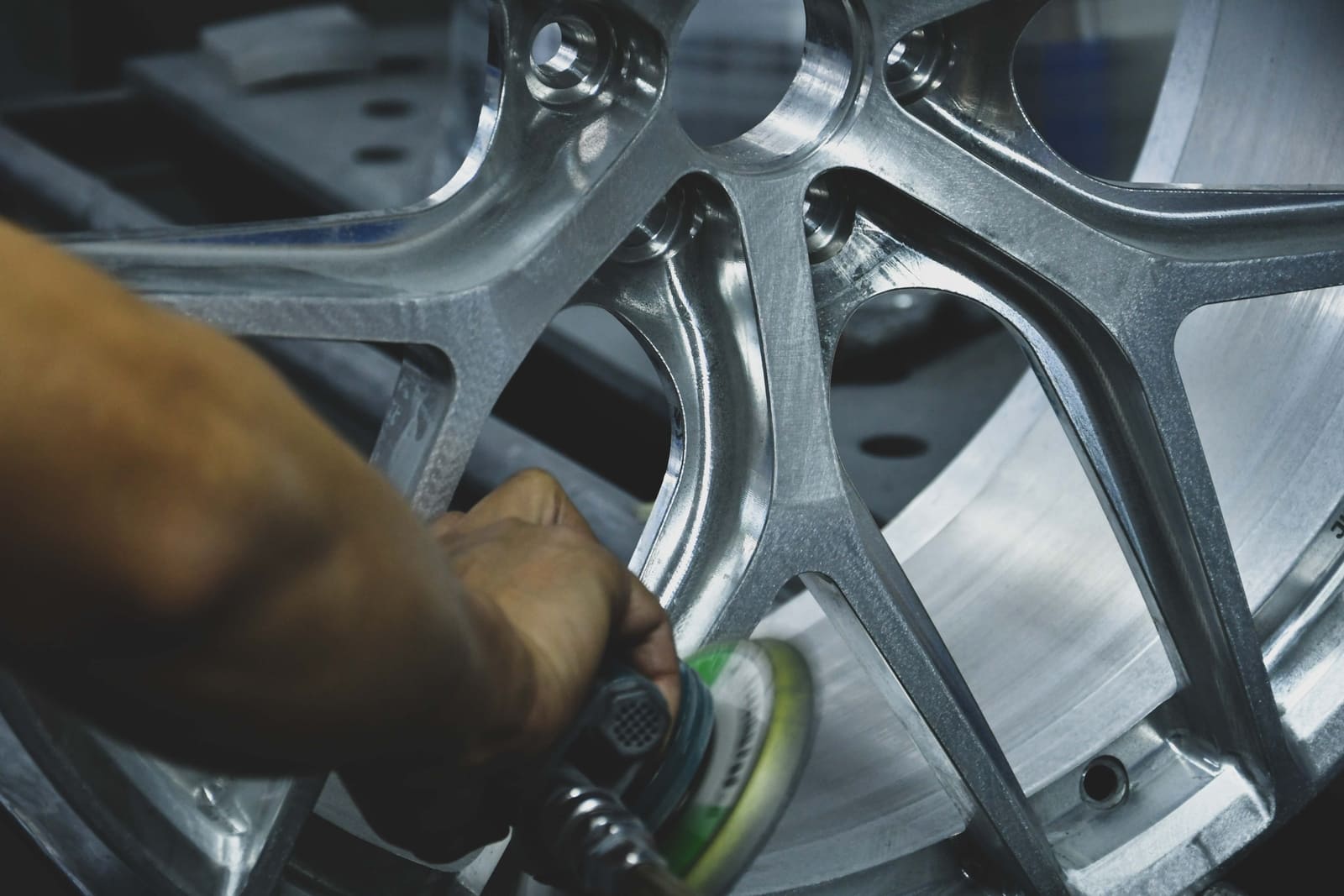
Figure 2. After milling is complete, the artisan hand-cleans the wheel surface to prepare the wheel for finishing.
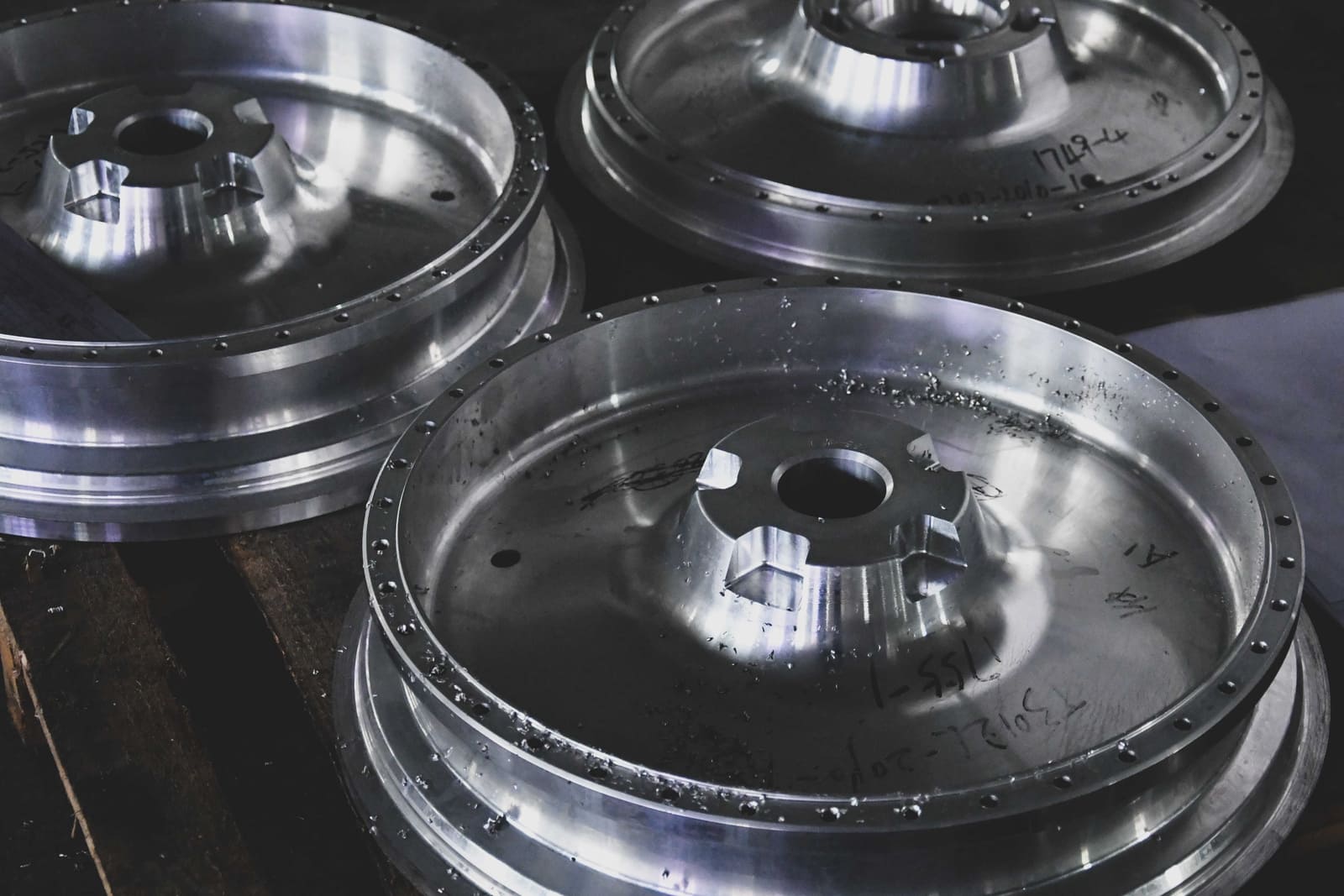
Figure 3. Centre-piece of multi-piece modular wheel – milling of the weight reduction pockets was completed.
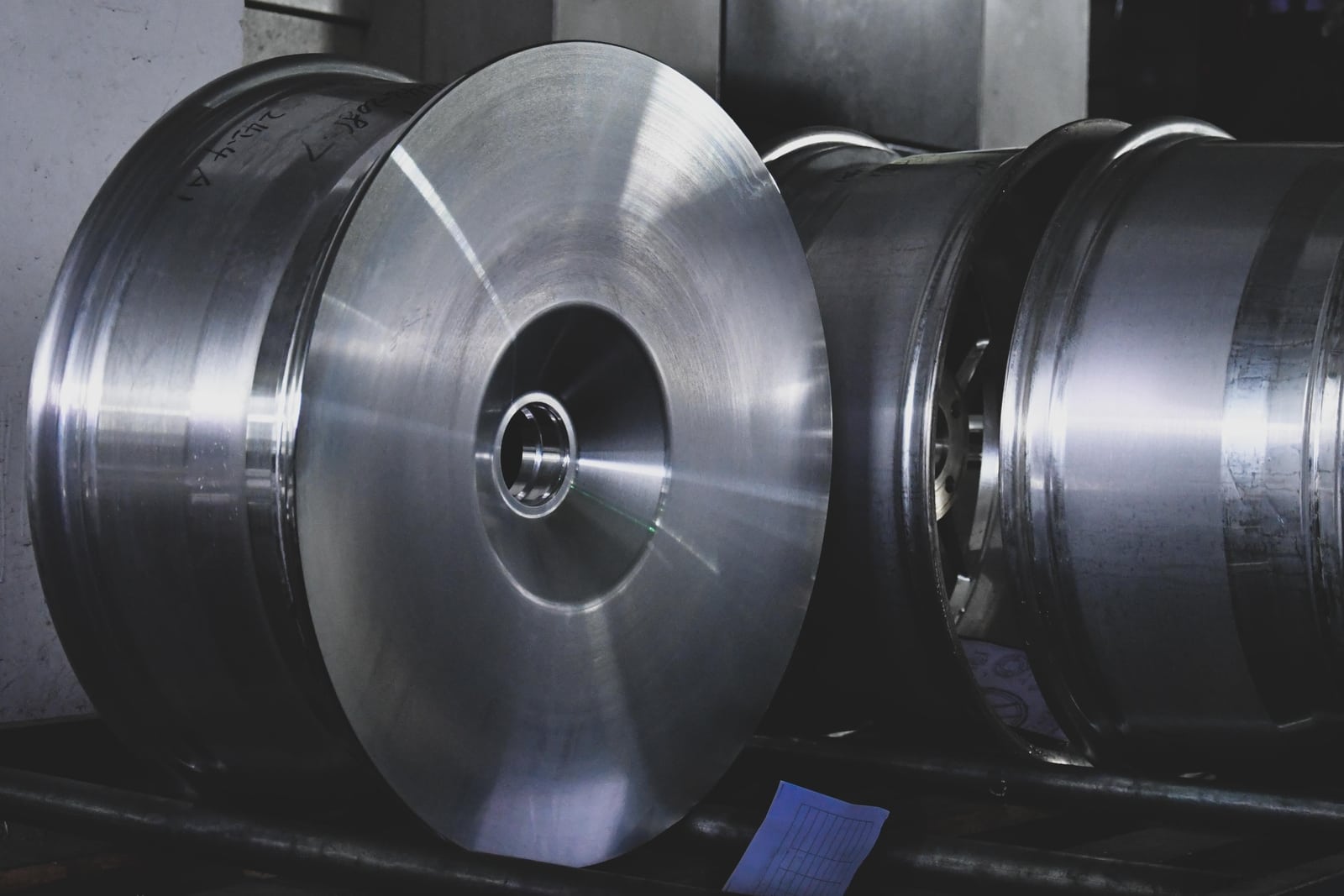
Figure 4. Forgings after the initial lathe process. Next, the spoke details will be milled out.
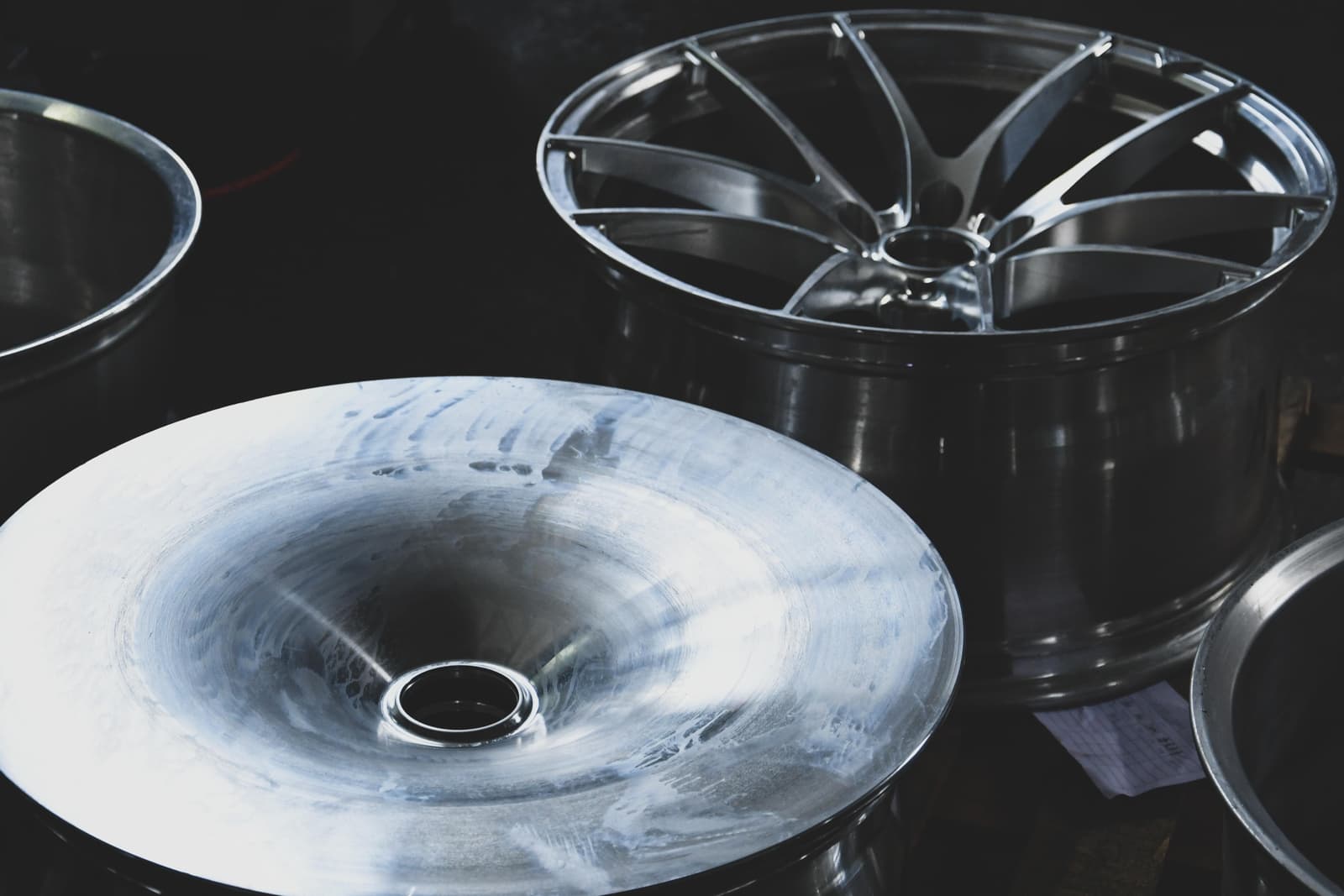
Figure 5. A lathed forging next to a freshly milled out wheel.
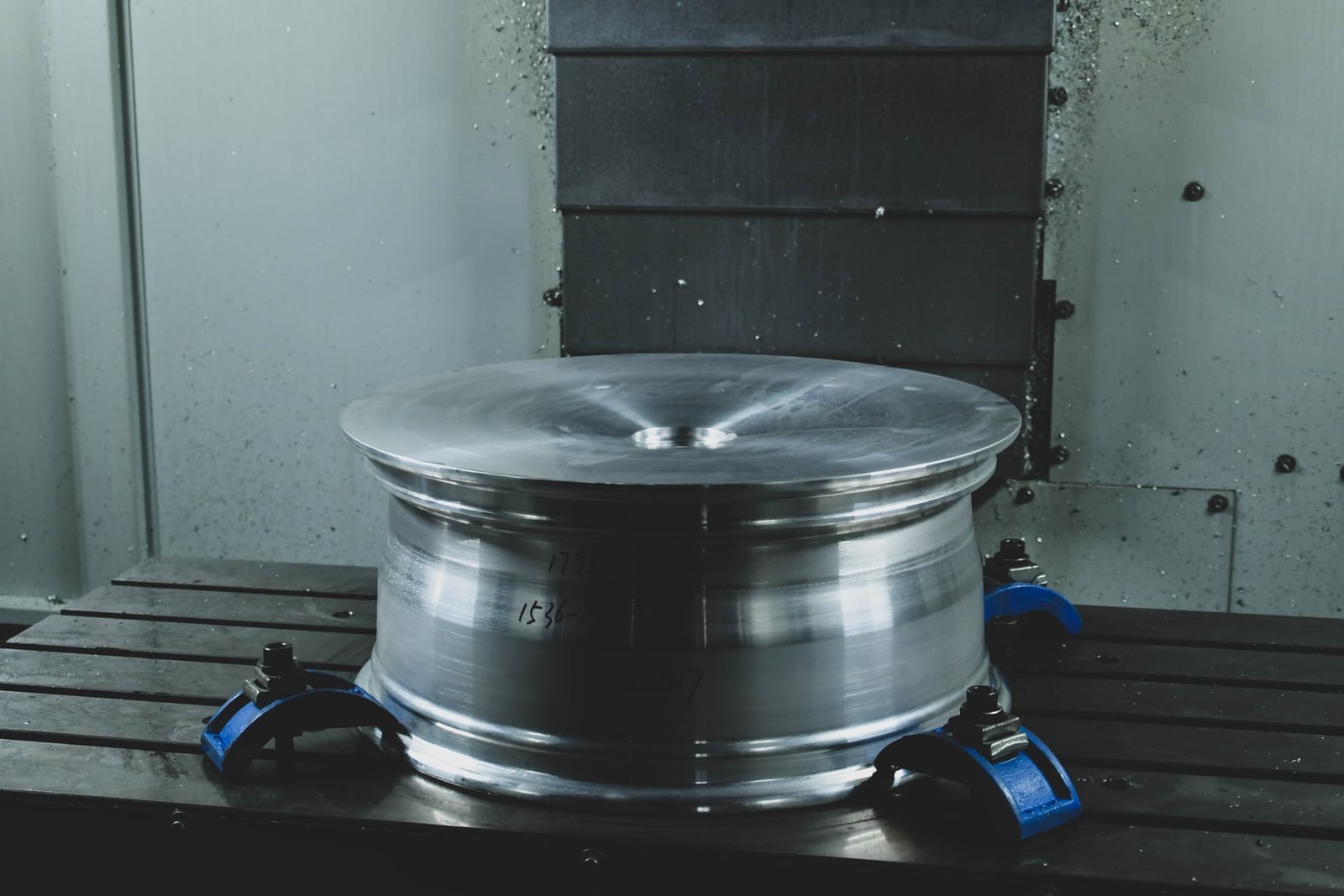
Figure 6. Forgings set up in the CNC milling centre, waiting to be processed.
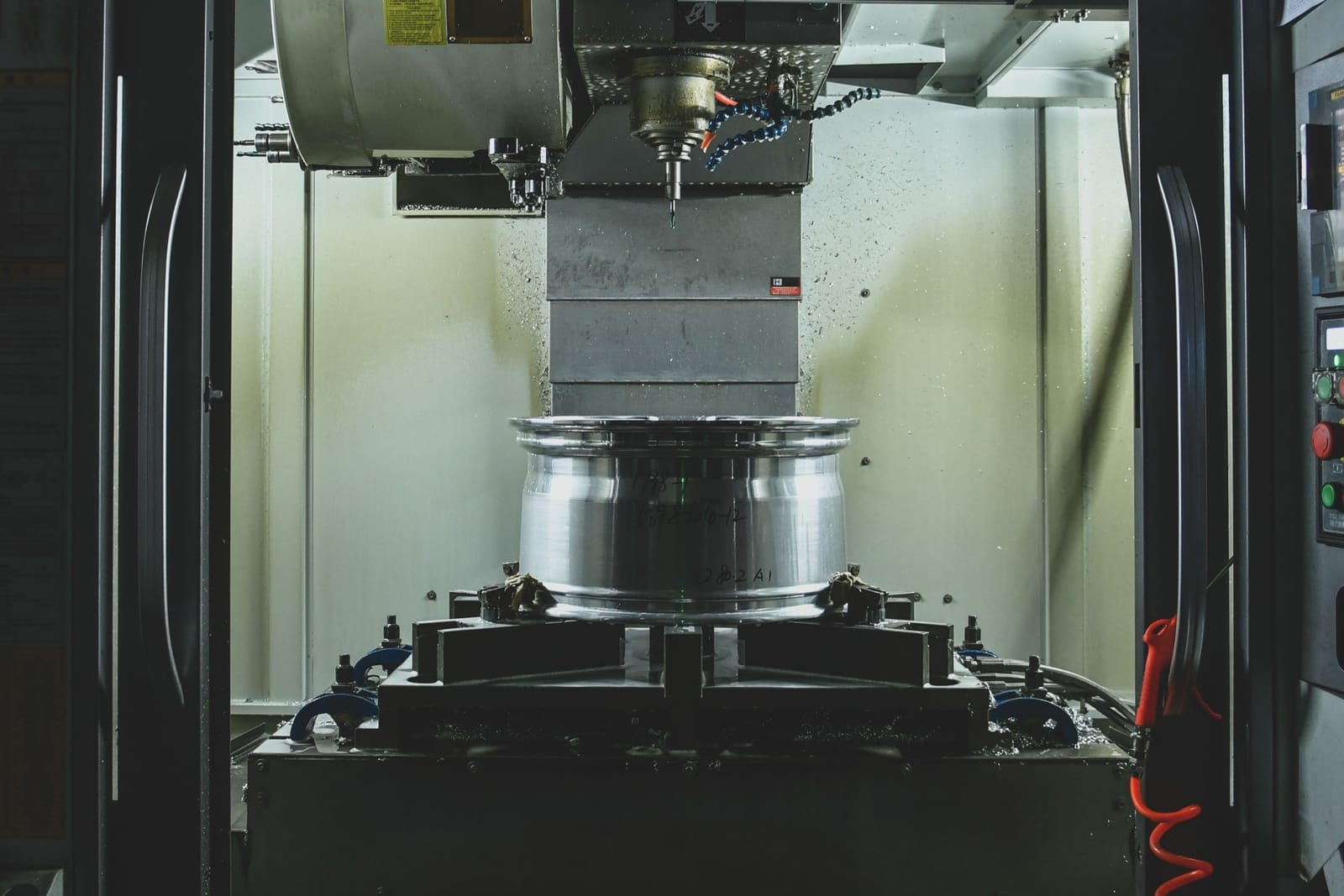
Figure 7. Freshly milled out wheel inside the vertical milling centre.
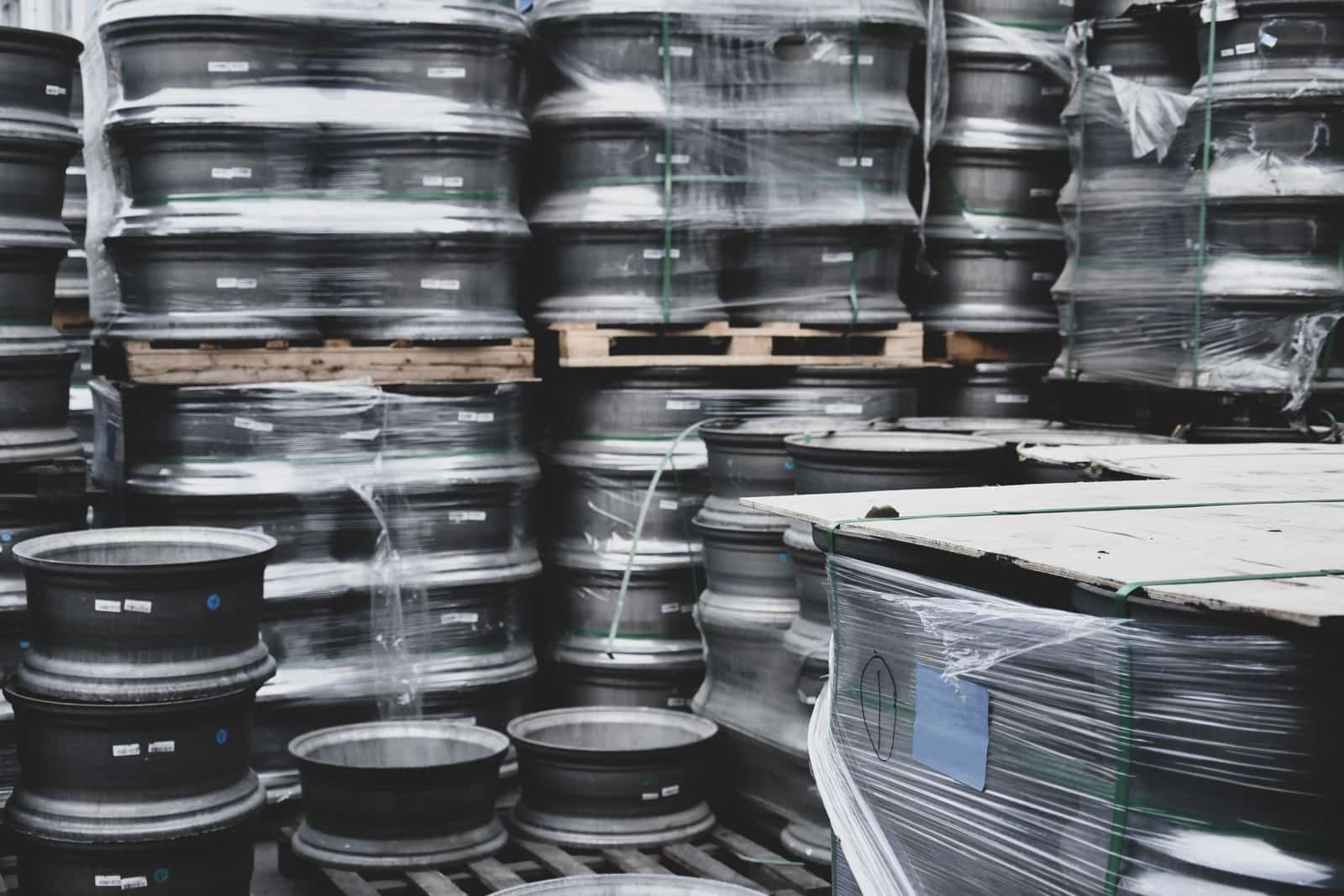
Figure 8. A well-stocked forging storage area.
GET IN TOUCH & Get A FREE QUOTE
Ready to make your own set of wheels? Send us a message about your Bespoke Forged Project idea for a free quote, and to discuss your idea – we love hearing them! Fields marked with an asterisk (*) are required.